私たちはお客様のニーズにベストパフォーマンスでお応えするため、
最新鋭の設備や技術を取り入れながら、常に品質向上に努めてきました。
加工設備一覧
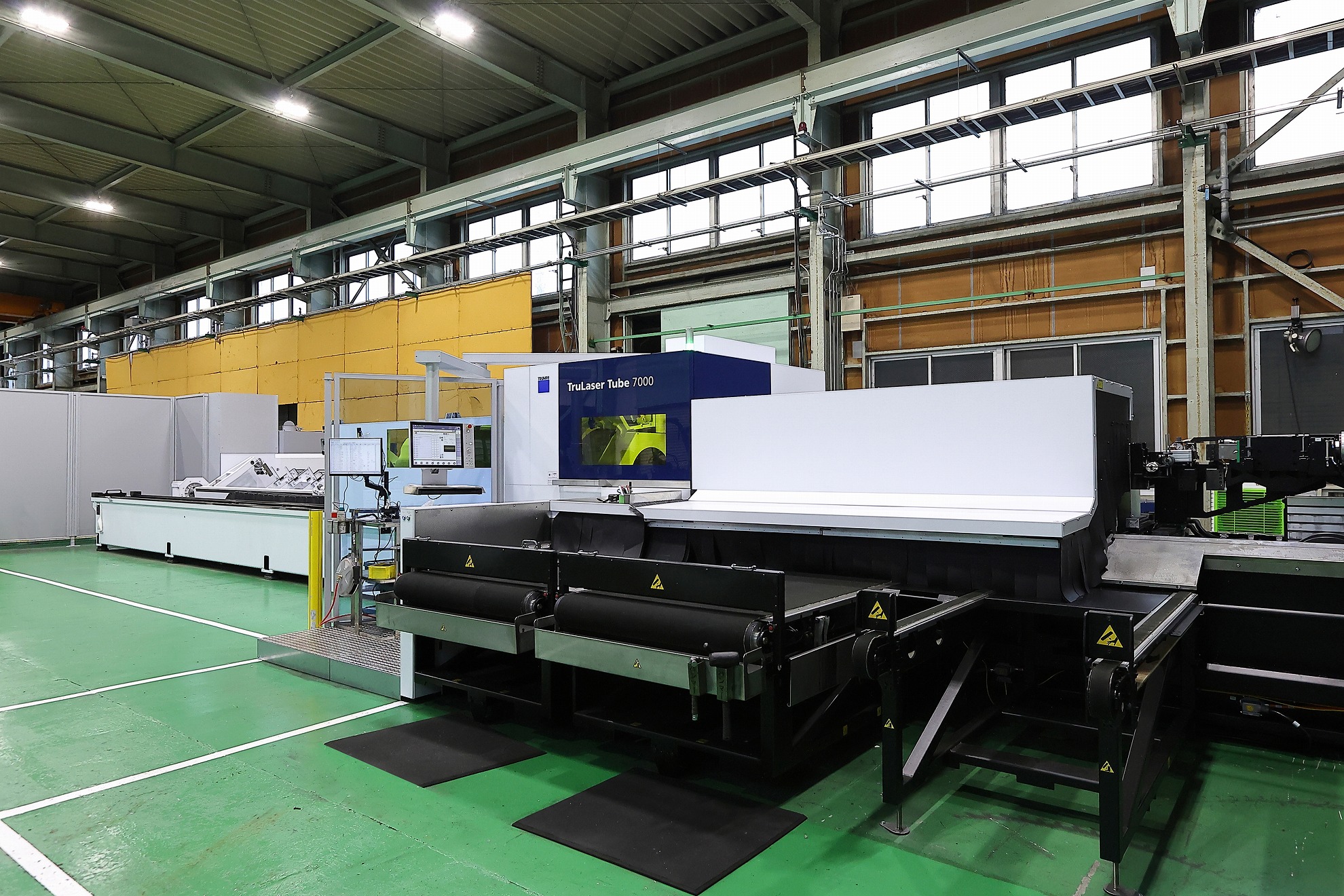
[レーザーパイプカッティングマシン]
TRUMPF TruLaser Tube 7000 fiber
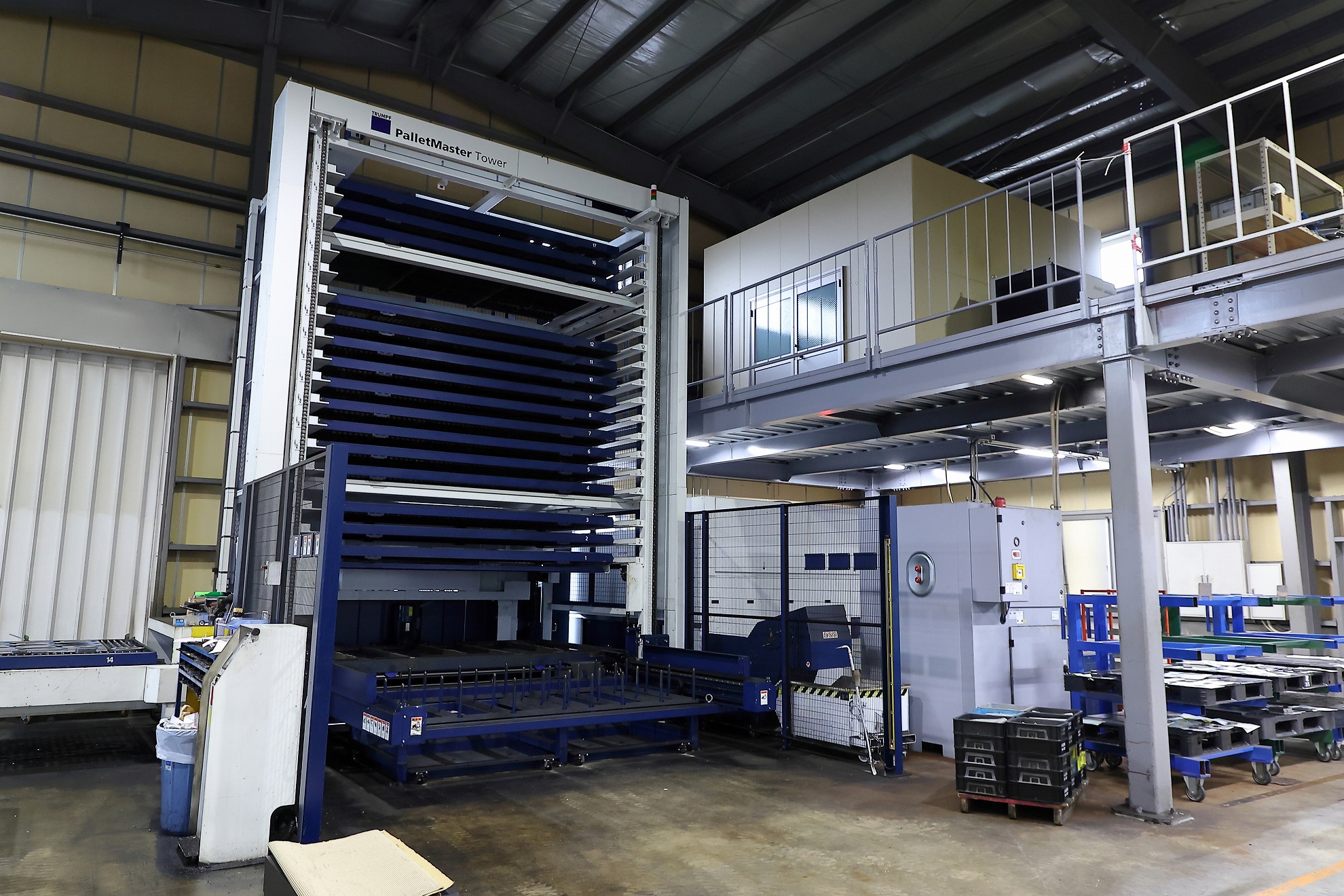
[2次元レーザー切断機 ]
TRUMPF TruLaser 5030 fiber+PalletMaster
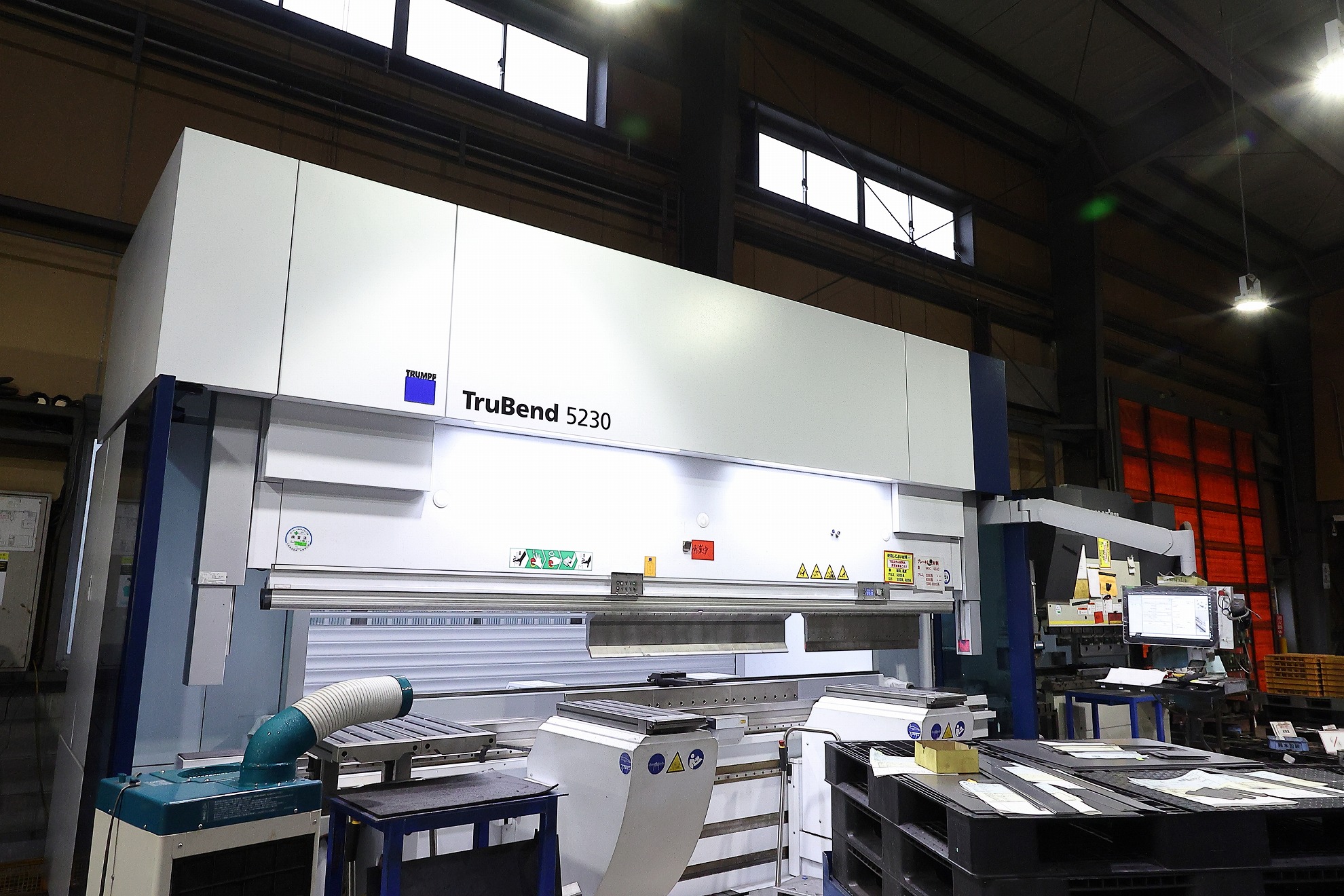
[4m対応,角度センサー搭載ベンダー]
TRUMPF TruBend 5230
設備名 | メーカー | 型式 | 台数 |
---|---|---|---|
3D パイプレーザー切断機 | TRUMPF | TruLaser Tube 7000 fiber (4.0KW) | 1台 |
3D パイプレーザー切断機 | TRUMPF | TruLaser Tube 7000(3.6KW) | 1台 |
2Dファイバーレーザー切断機 | TRUMPF | TruLaser 5030 fiber(8KW) | 1台 |
2Dファイバーレーザー切断機 | TRUMPF | TruLaser 5030 fiber(5KW) | 2台 |
プレスブレーキ | TRUMPF | TruBend 5230(4m対応) | 1台 |
プレスブレーキ | TRUMPF | TruBend 5130 | 1台 |
プレスブレーキ | TRUMPF | TruBend 5085 | 1台 |
プレスブレーキ | コマツ | PAS5020 | 1台 |
ファイバーレーザー溶接機 | レーザックス | OPTICEL FH-450 | 1台 |
YAGレーザー溶接機 | 日本ウェルディング | PLS-P40 | 1台 |
アーク溶接ロボットセル | TRUMPF | TruArc Weld 1000 | 1台 |
溶接ロボット(TIG) | Panasonic | 各種 | 1台 |
溶接ロボット(CO2) | Panasonic | 各種 | 3台 |
TIG溶接機 | Panasonic | 各種 | 6台 |
半自動溶接機 | Panasonic | 各種 | 15台 |
スポット溶接機 | ダイヘン | SLAI45-610 | 1台 |
プラズマ切断機 | ダイヘン | A-70 / A-50 | 5台 |
糸面取り機 | エステーリンク | メタルエステ1000/1300 | 各1台 |
工程のご紹介
レーザー・溶接・板金加工の高品質&短納期に対応いたします
短納期・高品質を支える「設計」
お客様からいただいた図面をまずはCADデータに変換し、続いて加工機用のCAMデータへの変換します。 当社ではこのデータ変換を約10人の専任設計者が行なっています。
さらに同一製品の図面を2人の設計者が作成し、データ作成完了後お互いの設計データを照らし合わせることで、設計ミスのチェック、品質管理、不良率低減などを目的とした2重チェック体制を整えています。
1日約300枚、月産7000種類の少量多品種を短納期かつ不良率1%以下のモノづくりを当社の約10人の設計チームが支えています。
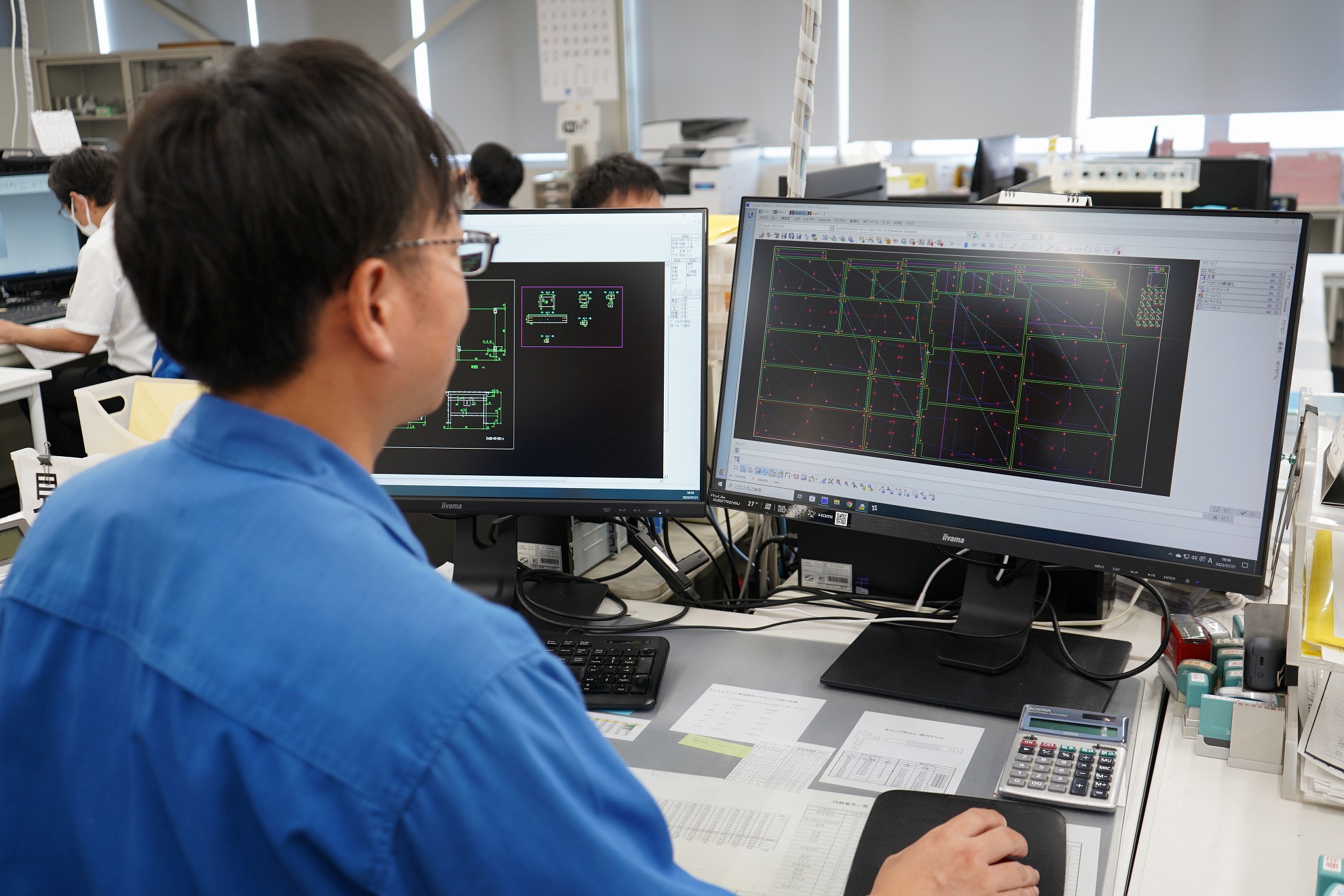
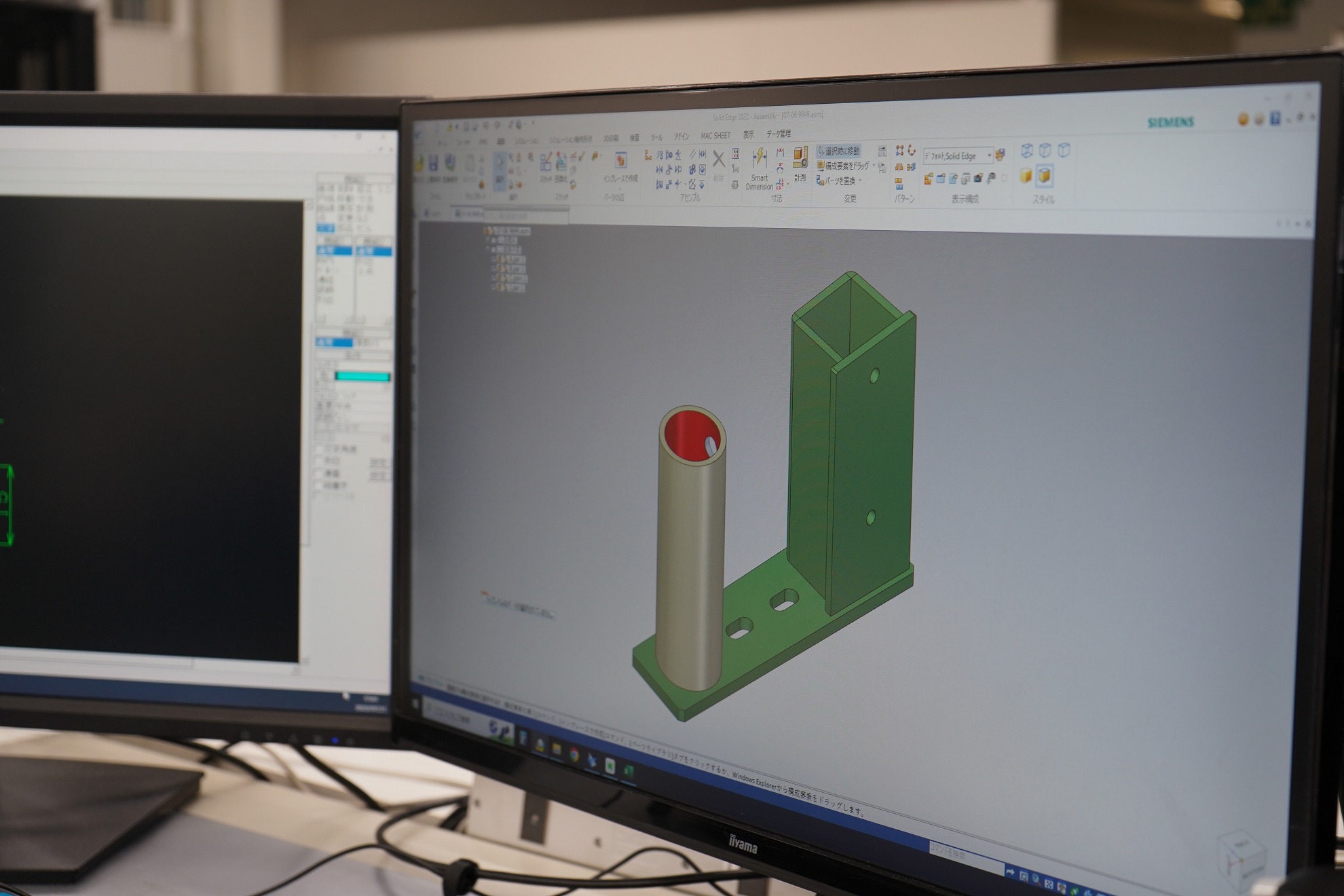
高品質・短納期対応の「レーザー加工」
当社のレーザー加工機の特徴は、8kWファイバーレーザー切断機、4kWパイプレーザー加工機をはじめとする最新鋭設備群を駆使した高品質の高速加工です。
これらの設備により銅、真鍮などの高反射材においてもレーザー加工が可能になり、短納期かつ切断面の綺麗なレーザー加工が可能です。
その他、材質、板厚、形状を考慮し、酸素から窒素に切り替えることで、生産スピード向上と低コスト化を図っています。さらに、3Dパイプレーザー加工機の効果的な活用による加工、製品の強度アップや、製品の用途に合わせた最適設計の 提案も得意としております。
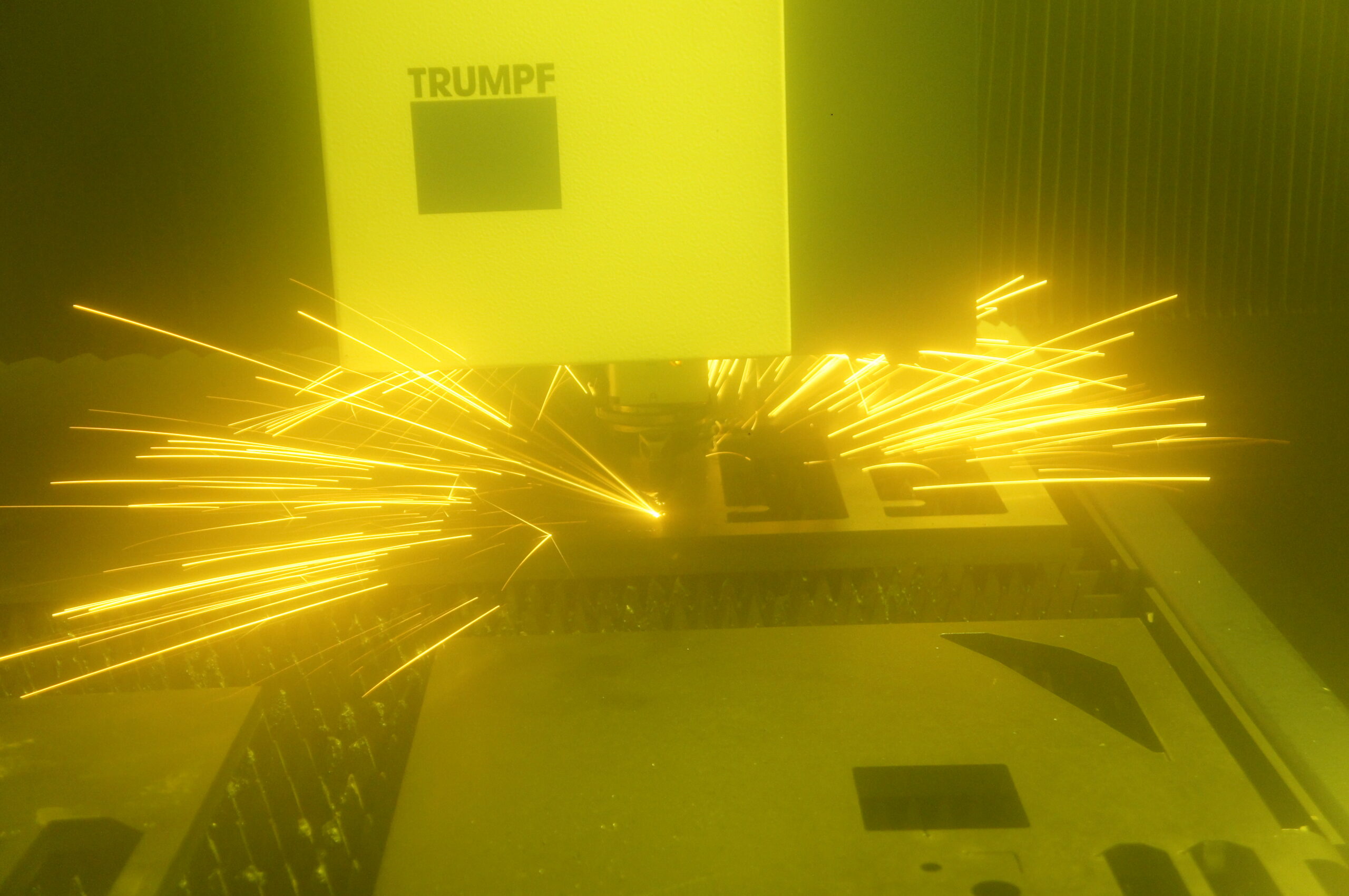
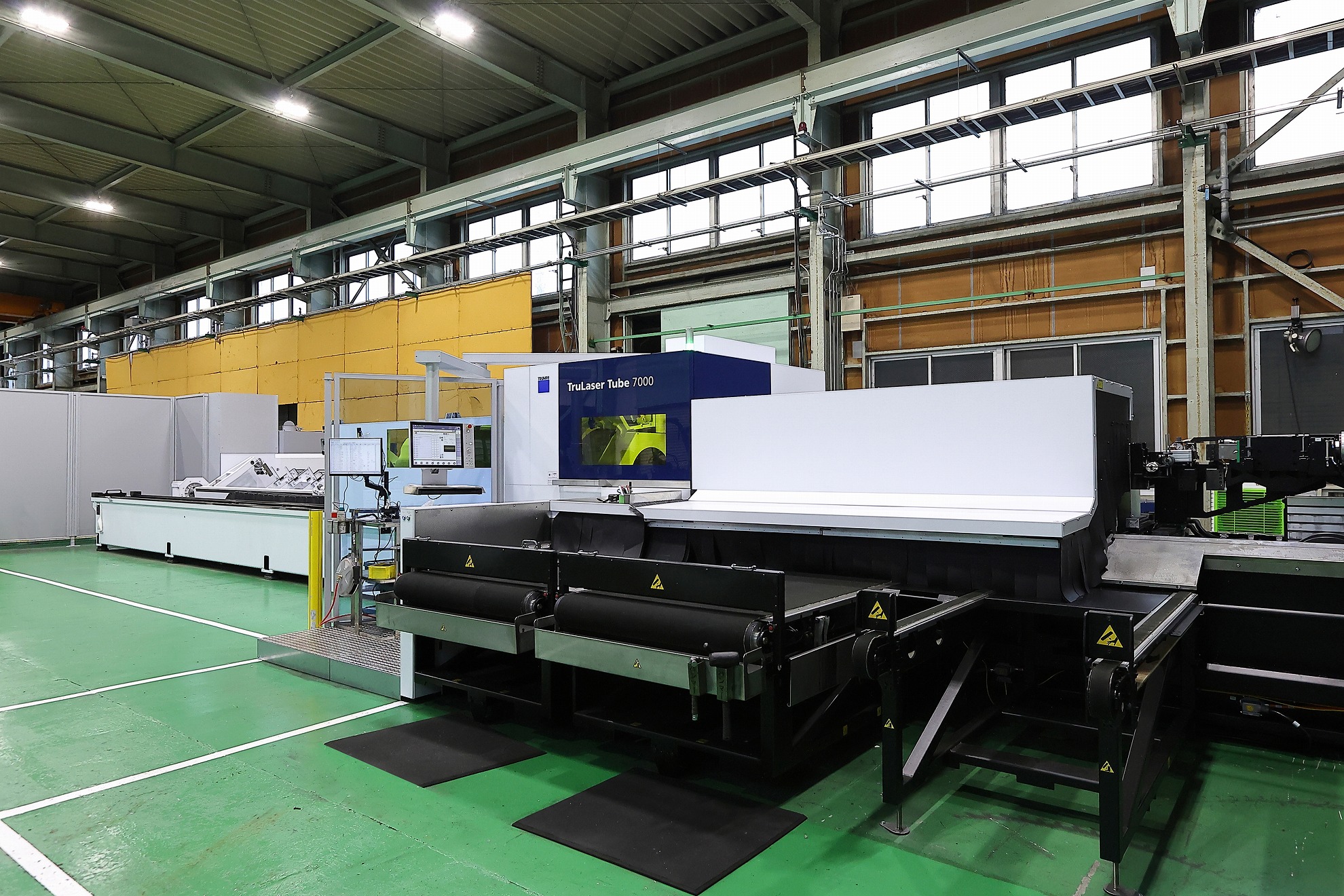
熟練工と充実した設備による曲げ加工
一般的には熟練工の経験が必要とされる曲げ工程に、長さ4m対応をはじめとする角度センサー搭載の最新ベンダーを複数台導入しております。
これにより、角度センサーによる正確な角度出し、高い通り精度など品質面での高度化に成功。最新機器を活かす技術者たちが、ジョブショップとして「少量多品種生産」を実現。だからこその最高効率、高品質・スピード生産を実現しています。
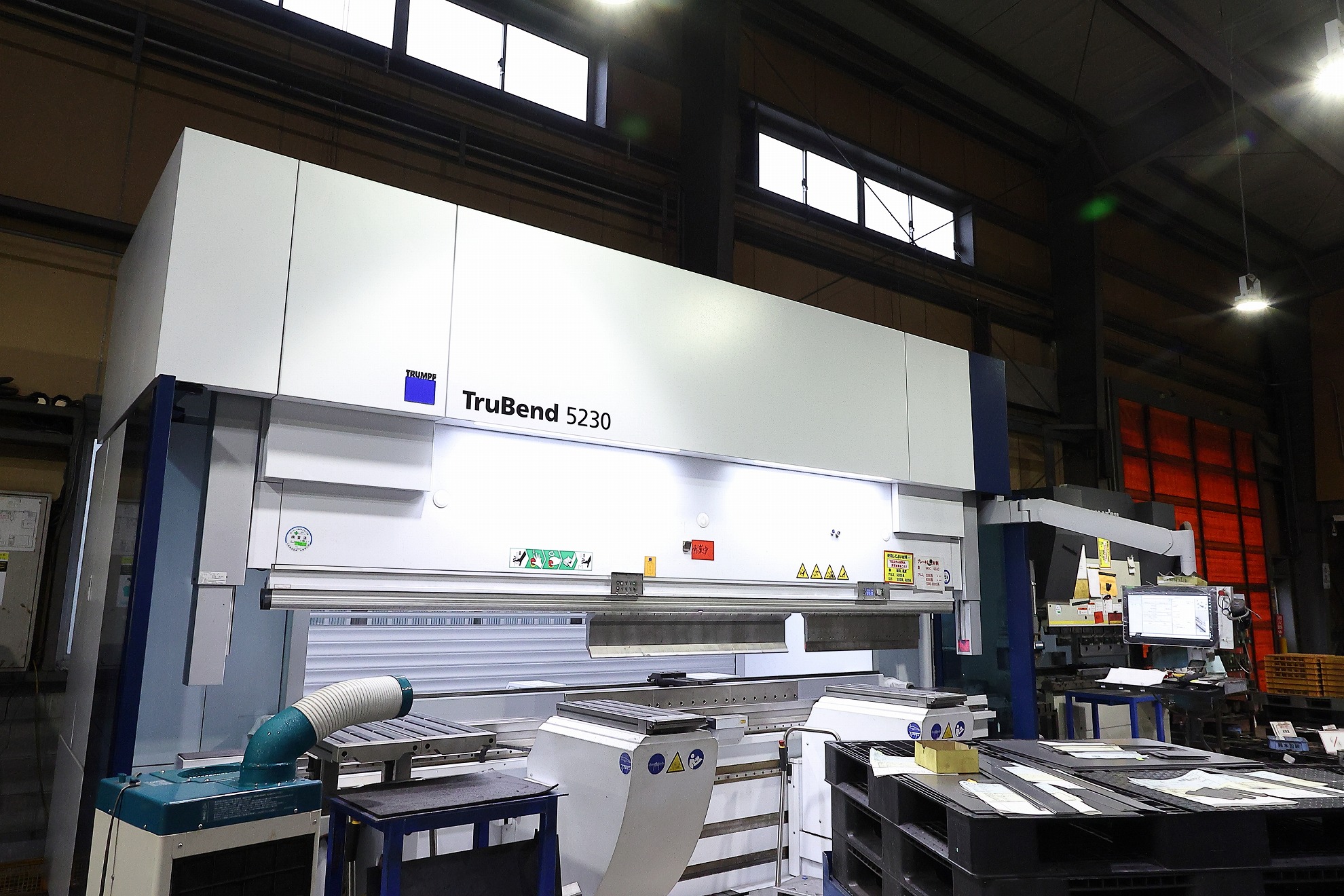
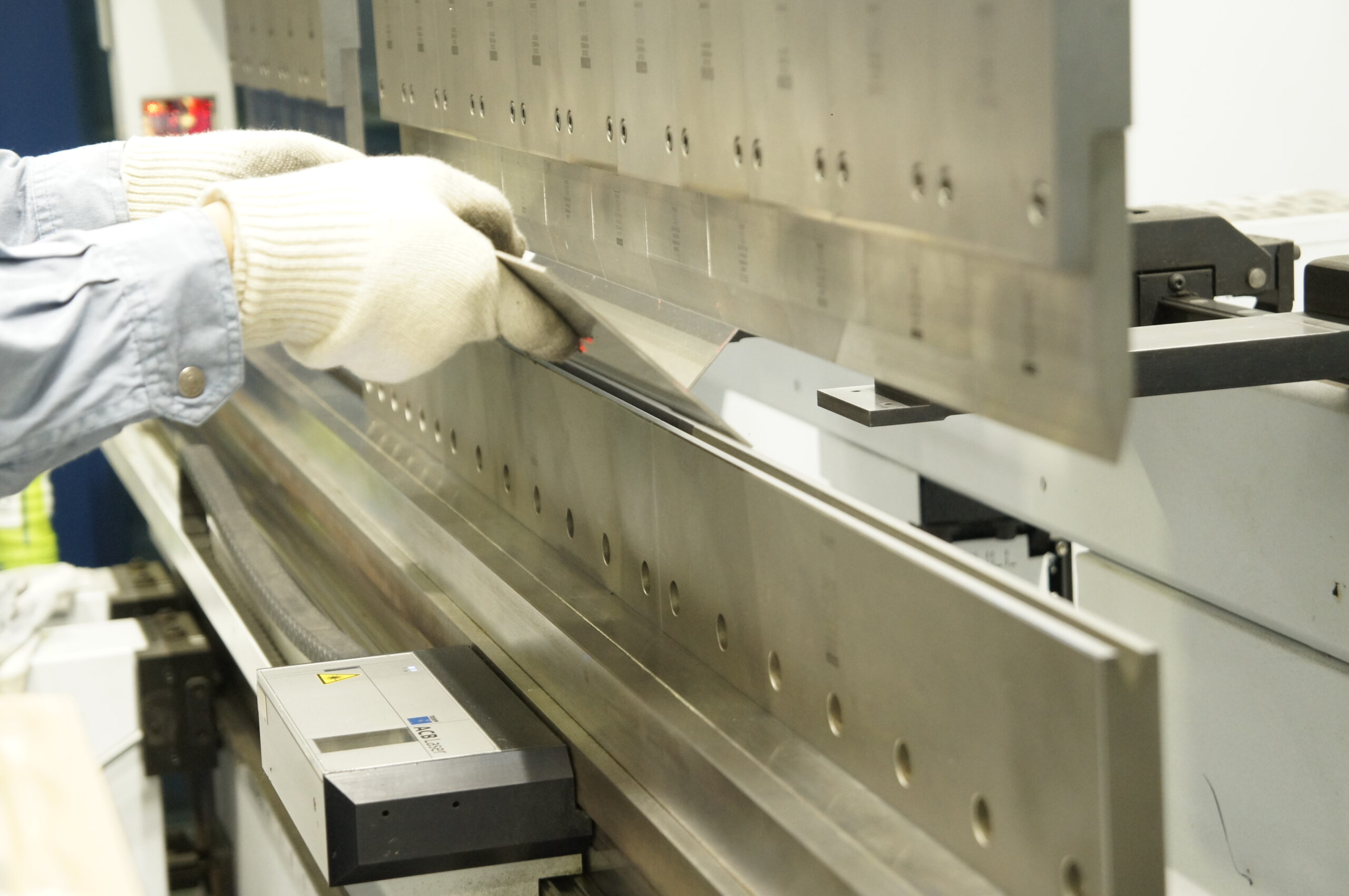
熟練工と充実した設備による溶接技術
フルデジタル溶接機による低ひずみ・低スパッタ・溶接焼け低減の取組や、溶接ロボットと半自動溶接機による量産の効率化に加え、2019年には最新の450wファイバーレーザー溶接機器を導入。ステンレスや鉄鋼材の薄板においてもひずみや溶接焼けを限りなく低減し、幅広い加工に対応可能です。また、特に溶接条件が困難とされるアルミ溶接も行なっており、熟練工と最新機器による相乗効果で高い溶接技術を生み出し、短納期・高品質を実現しています。
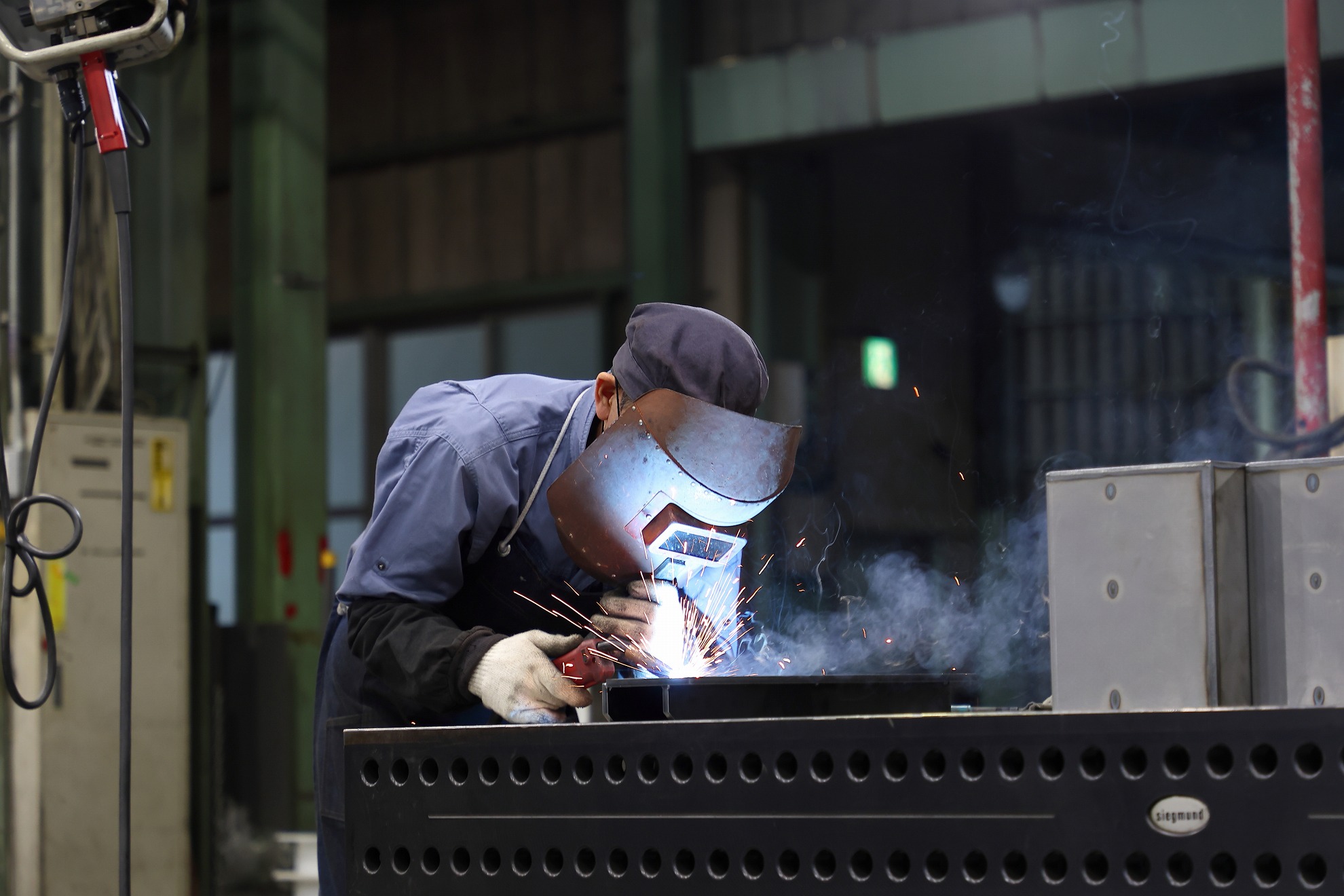
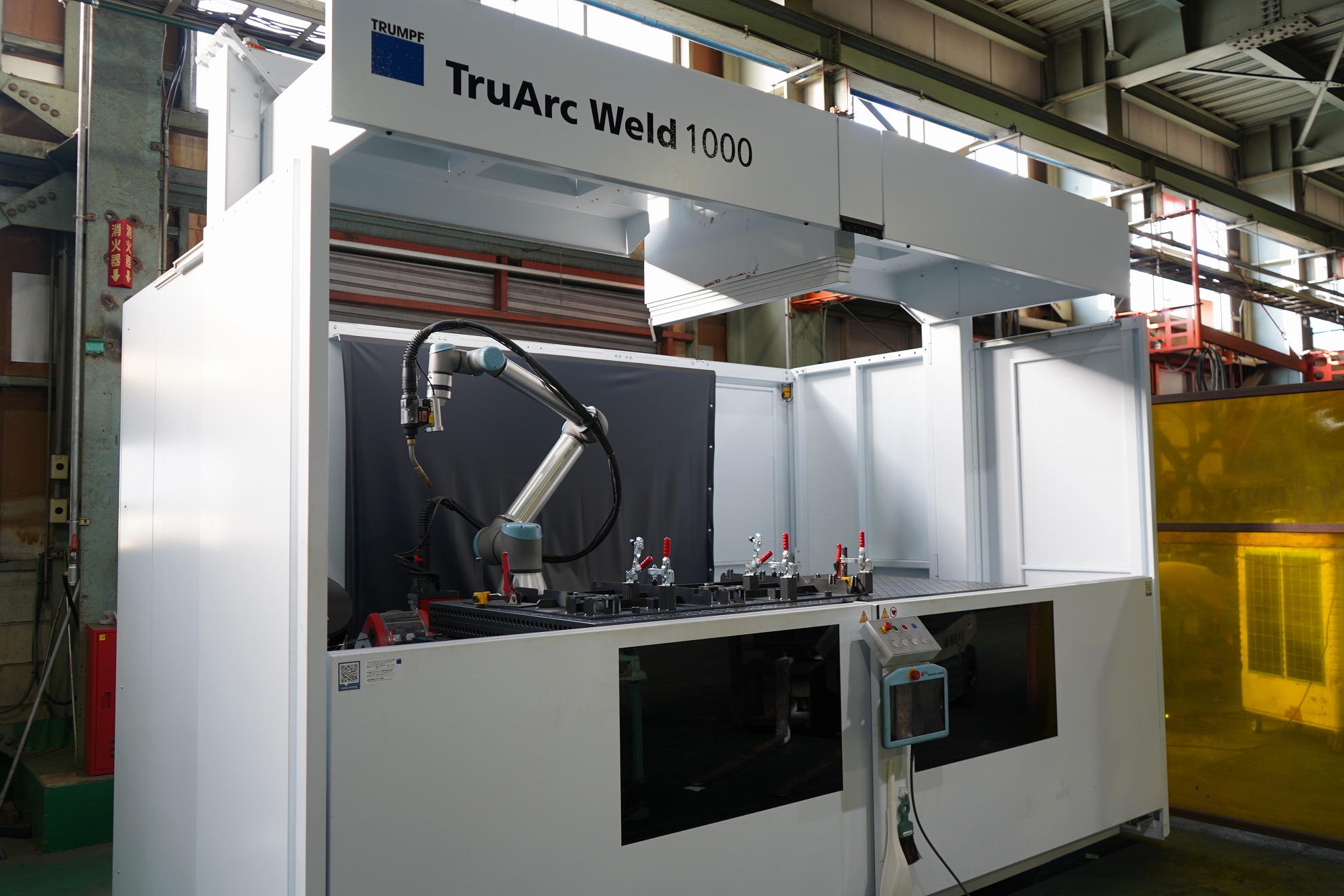
仕上・組み上げ
仕上工程では、溶接により発生した熱ひずみや溶接焼けの除去、グラインダーによるバリ取り作業や表面仕上げなど仕上げを行い、その後、発注内容に応じて組み立て作業や、角加工、各種サイズのネジ穴加工を行います。製品の仕上品質向上と作業効率向上の為、糸面取り機を複数台導入済です。
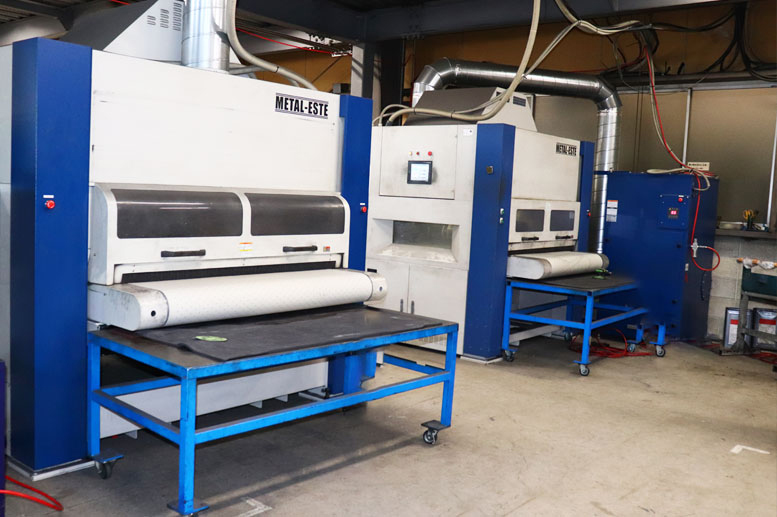
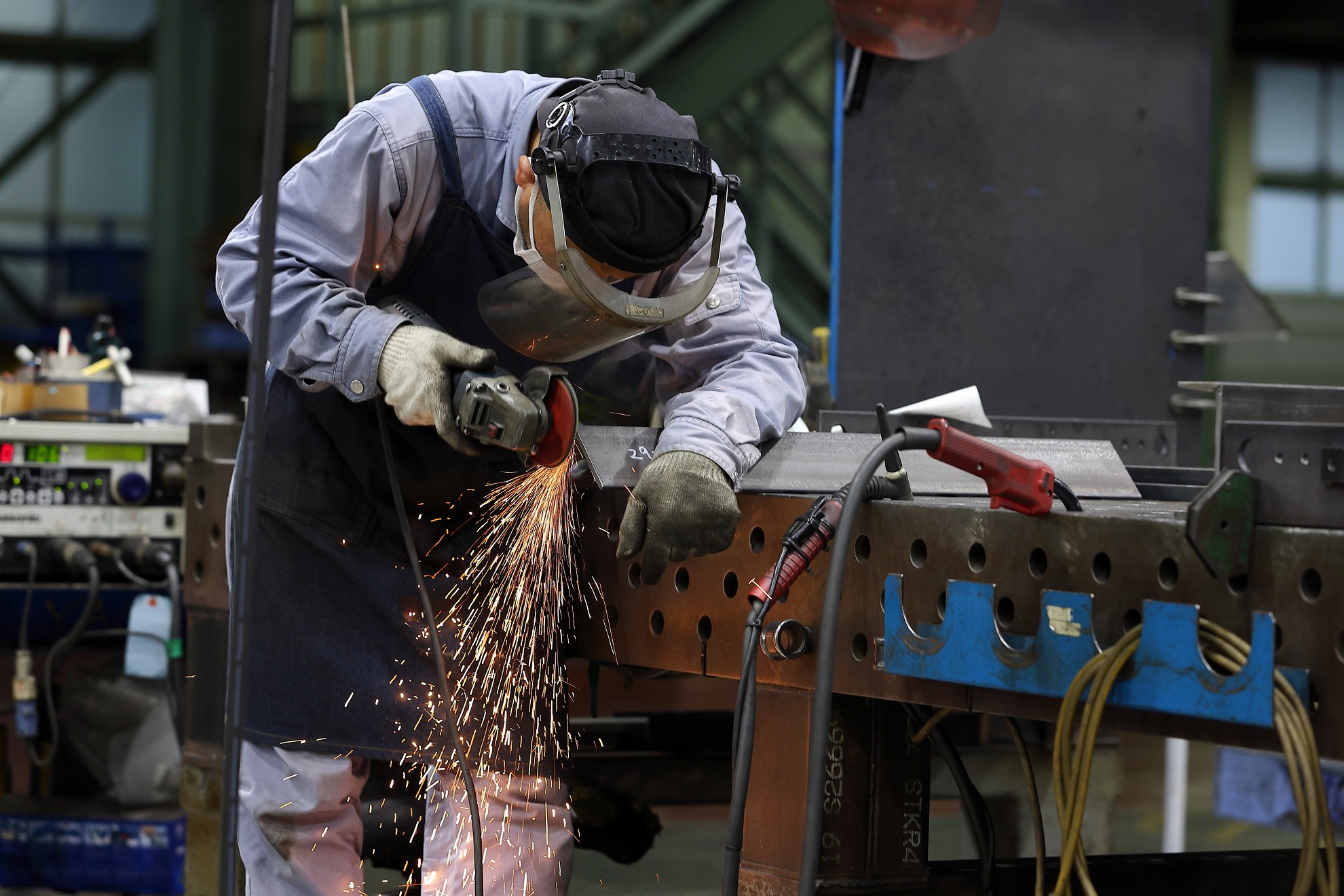
検査・出荷・納期と品質管理
当社独自の品質管理システムにより、設計の段階でのCAD/CAMデータ作成時における二重チェック、作りこみおける工程内検査と出荷前検査を併用し、徹底する事で、不良率1%以下の高品質生産を実現しております。お客様の希望納期にあわせた生産・配送計画にあわせて、当社社員のドライバーが大切な製品をお客様のもとへお届け致します。お急ぎのお客様は当社にて引き取り対応も可能です。
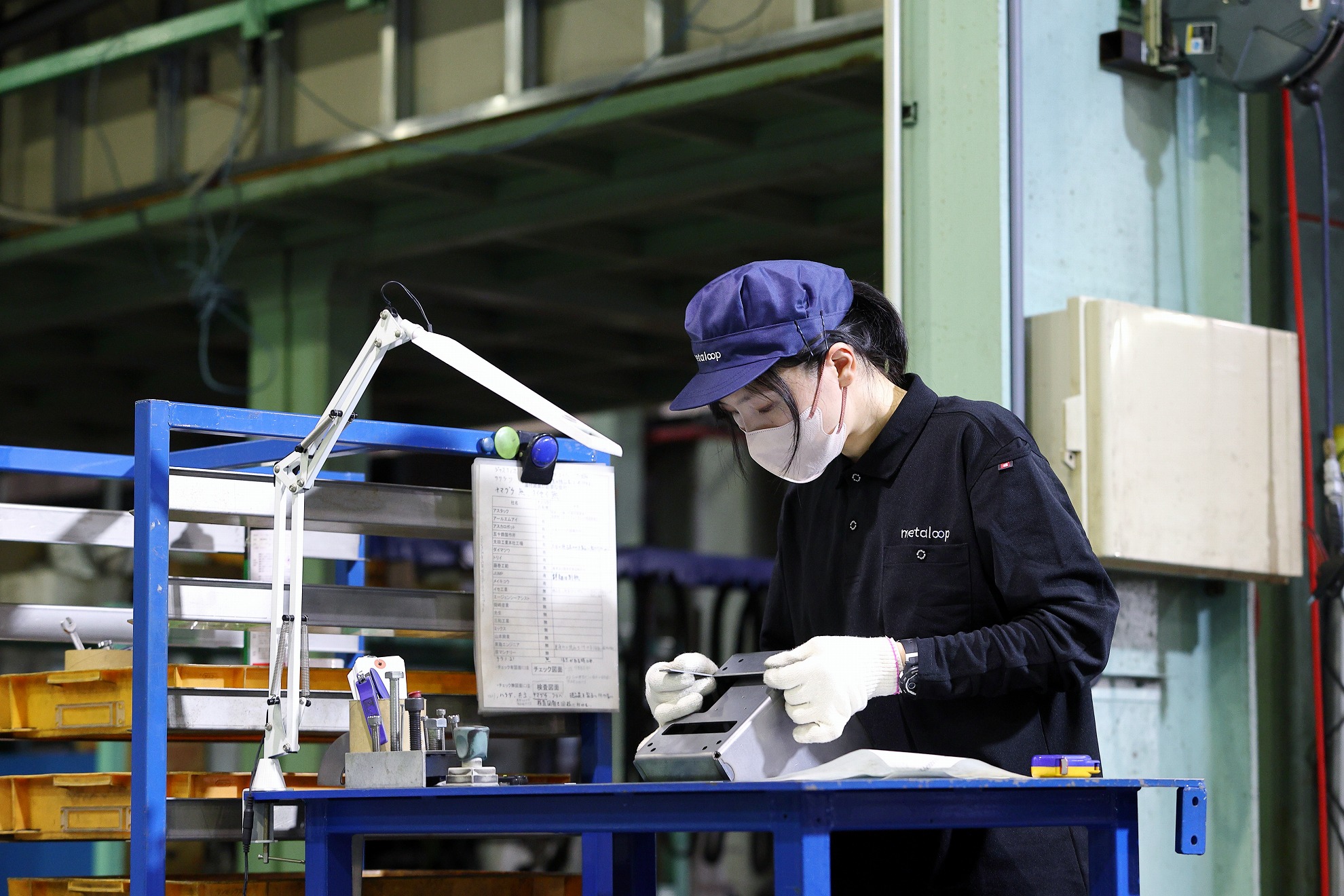
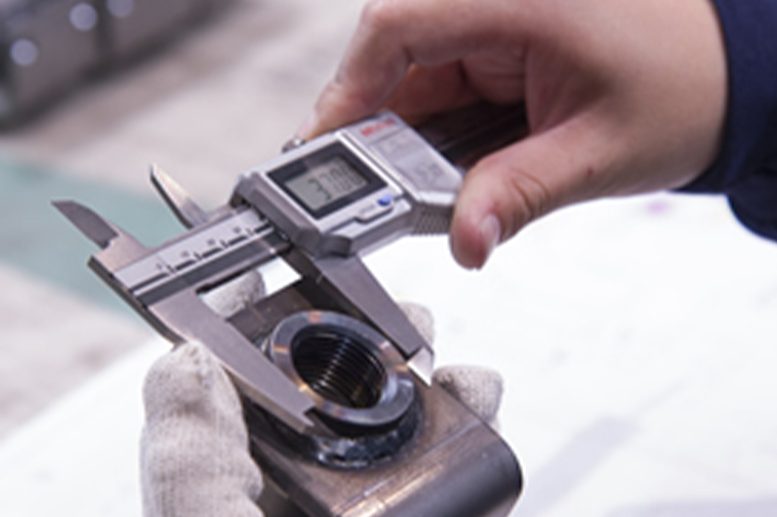